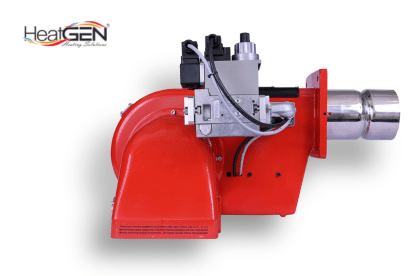
In the world of industrial heating, efficiency and precision are king. That’s where two-stage gas burners come in. These innovative burners offer a unique approach to combustion, delivering a powerful combination of fuel efficiency and precise temperature control.
For industrial burner operators, understanding the two-stage combustion process is key to maximizing the performance of your equipment. Let’s delve into the world of two-stage gas burners and explore how they work.
The Two-Stage Advantage
Unlike traditional single-stage burners that operate at a constant flame size, two-stage gas burners offer a more nuanced approach. They feature two distinct firing rates:
- Low Stage: This stage provides a lower intensity flame, ideal for maintaining pilot light operation or for situations requiring minimal heat.
- High Stage: When additional heat is needed, the burner kicks into the high stage, delivering a more powerful flame.
This two-stage functionality offers several advantages:
- Improved Efficiency: By utilizing the low stage during periods of lower heat demand, two-stage gas burners significantly reduce fuel consumption compared to single-stage burners.
- Enhanced Temperature Control: The ability to precisely adjust the flame size allows for more precise control over the heating process, reducing fluctuations and ensuring consistent product quality.
- Reduced Emissions: The efficient combustion process of two-stage gas burners often leads to lower emissions of pollutants like nitrogen oxides (NOx).
How it Works
The inner workings of a two-stage gas burner involve a valve system that regulates the flow of gas to the burner head. In the low stage, the valve restricts gas flow, resulting in a smaller flame. When a high stage is activated, the valve opens wider, allowing for a larger and more intense flame.
Modern two-stage gas burners often integrate with advanced control systems. These systems can automatically adjust the firing stage based on pre-programmed temperature settings or real-time process needs.
Applications for Two-Stage Gas Burners
The versatility of two-stage gas burners makes them suitable for a wide range of industrial applications, including:
- Industrial Boilers: Both hot water and steam boilers can benefit from the efficiency and precise temperature control offered by two-stage burners.
- Process Heating: Applications requiring consistent and controllable heating, such as drying, curing, and asphalt production, can leverage the two-stage functionality for optimal results.
- Food Processing: In the food and beverage industry, precise temperature control is crucial. Two-stage gas burners provide the necessary control for tasks like cooking, baking, and pasteurization.
Optimizing Performance
Regular maintenance is essential to maximize the performance of your two-stage gas burner. This includes:
- Inspections: Regularly inspect the burner head and gas valve system for signs of wear or damage.
- Cleaning: Periodically clean the burner head to remove any buildup of soot or debris that could hinder performance.
- Calibration: Ensure your control system is properly calibrated to maintain accurate temperature control.
By understanding the two-stage combustion process and implementing proper maintenance practices, industrial burner operators can leverage the many benefits of two-stage gas burners, achieving greater efficiency, improved temperature control, and reduced emissions in their operations.