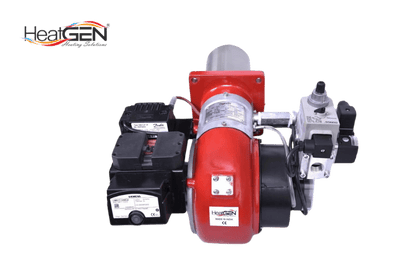
Industrial gas burners are essential components of various manufacturing processes, providing heat for tasks such as drying, heating, and combustion. As technology continues to advance, so too does the field of industrial gas burner technology. This blog post will explore some of the key trends shaping the future of this industry, including advancements in efficiency, emissions reduction, and automation.
Efficiency and Energy Conservation
One of the most pressing concerns in today’s world is energy conservation. Industrial gas burners, as energy-intensive equipment, are under increasing scrutiny to improve their efficiency. Several trends are emerging to address this challenge:
- Advanced Combustion Technology: Manufacturers are developing burners with more efficient combustion processes, such as staged combustion and lean premixed combustion. These techniques reduce heat loss and improve fuel utilization, resulting in lower energy consumption.
- Intelligent Burner Controls: Modern burners are equipped with sophisticated control systems that can optimize burner performance based on real-time operating conditions. These systems can adjust fuel-air ratios, flame shape, and other parameters to ensure maximum efficiency.
- Modular Burner Design: Modular burners allow for flexibility and scalability, enabling manufacturers to tailor burner systems to specific process requirements. This can help to reduce energy consumption by avoiding oversizing or undersizing burners.
Emissions Reduction
Environmental concerns are also driving innovation in industrial gas burner technology. Reducing emissions of pollutants such as nitrogen oxides (NOx) and carbon monoxide (CO) is a top priority for many industries. Here are some of the strategies being employed:
- Low-NOx Burners: These burners incorporate design features and combustion strategies that minimize the formation of NOx. Techniques such as staged combustion and selective catalytic reduction (SCR) are commonly used to achieve low-NOx emissions.
- Ultra-Low-NOx Burners: Ultra-low-NOx burners can be employed for applications with stringent emissions requirements. These burners often combine multiple emissions reduction technologies to achieve extremely low NOx levels.
- CO Reduction: While CO emissions are generally lower than NOx, efforts are also being made to further reduce them. Advanced burner designs and proper combustion tuning can help to minimize CO formation.
Automation and Digitalization
Automation and digitalization are transforming the industrial sector, and industrial gas burner technology is no exception. The following trends are shaping the future of burner automation:
- Predictive Maintenance: By leveraging data analytics and sensors, burner manufacturers can predict potential maintenance issues before they occur. This proactive approach can help to reduce downtime and improve overall burner reliability.
- Remote Monitoring and Control: Remote monitoring systems allow operators to monitor burner performance and make adjustments from a central location. This can improve efficiency and reduce the need for on-site personnel.
- Integration with Industry 4.0: Industrial gas burners are increasingly being integrated into Industry 4.0 ecosystems. This enables seamless communication with other equipment and systems, facilitating data-driven decision-making and process optimization.
Conclusion
A strong focus on efficiency, emissions reduction, and automation marks the future of industrial gas burner technology. As technology continues to evolve, we can expect to see even more innovative burner solutions that meet the growing demands of industries worldwide. By embracing these trends, manufacturers can improve their operational efficiency, reduce environmental impact, and stay competitive in today’s dynamic market.